Sikorsky Product History
Sikorsky S-76
Background
The S-76 was launched in the 1975 timeframe as the first Sikorsky model to be designed for commercial rather than military missions in order to increase the commercial portion of the company’s business. Its intended missions included the transport of workers to and from offshore oil rigs in a 12 passenger version and transport of business executives in a 6 passenger VIP version. Funding for its design, development and certification was provided from company sources. The technology basis for the S-76 was the Utility Tactical Transport Aircraft System (UTTAS) that had been awarded to Sikorsky in 1972. In particular, the rotor blade aerodynamic and structural features including blade airfoil, twist, swept tip and titanium spar were all embodied in the S-76. The UTTAS elastomeric main rotor head design as well as the cross beam bearingless tail rotor design was also applied to the S-76.
The Sikorsky S-76® is an intermediate class twin engine commercial helicopter powered by two turboshaft engines, which drive both the main and tail rotors, each with four blades. The S-76 landing gear is retractable.
The S-76 was announced at The HAA (now HAI) Convention in Las Vegas, Nevada in February 1975.
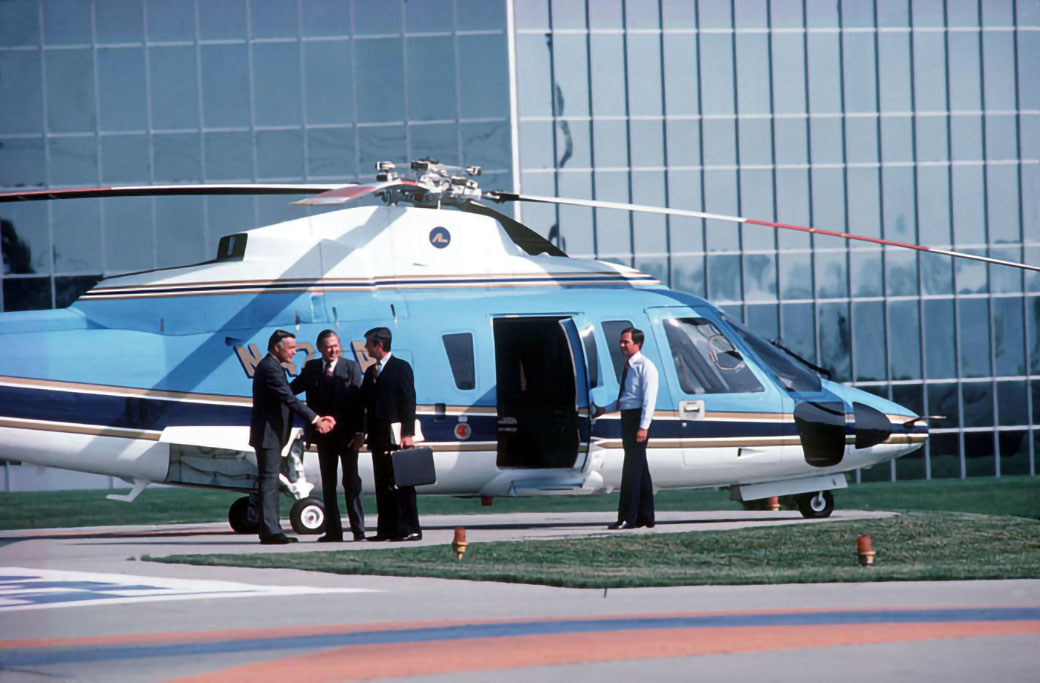
The sleek lines of the S-76 combined with significant advancements in rotor technologies and with improved engine fuel consumption, resulted in a helicopter having excellent efficiency.
The executive transport version was designed with a quiet cabin which would provide a work environment during flight and allow conversations without the need for headsets. The S-76 was designed to replace small business jets for short to medium business trips.
Sikorsky’s development of the UH-60 Black Hawk served as the basis for the S-74, which was later re-designated the S-76 Spirit in honor of the U.S. Bicentennial. The design accommodates 2 pilots and 12 passengers, to accommodate an oil rig crew change, and was initially powered by two Allison 250 C30 turboshaft engines of 650 shp (Takeoff Power) each. The prototype first flew on March 13, 1977. The name Spirit was officially dropped by the company on October 9, 1980 due to unanticipated complications when Spirit was translated into certain foreign languages.
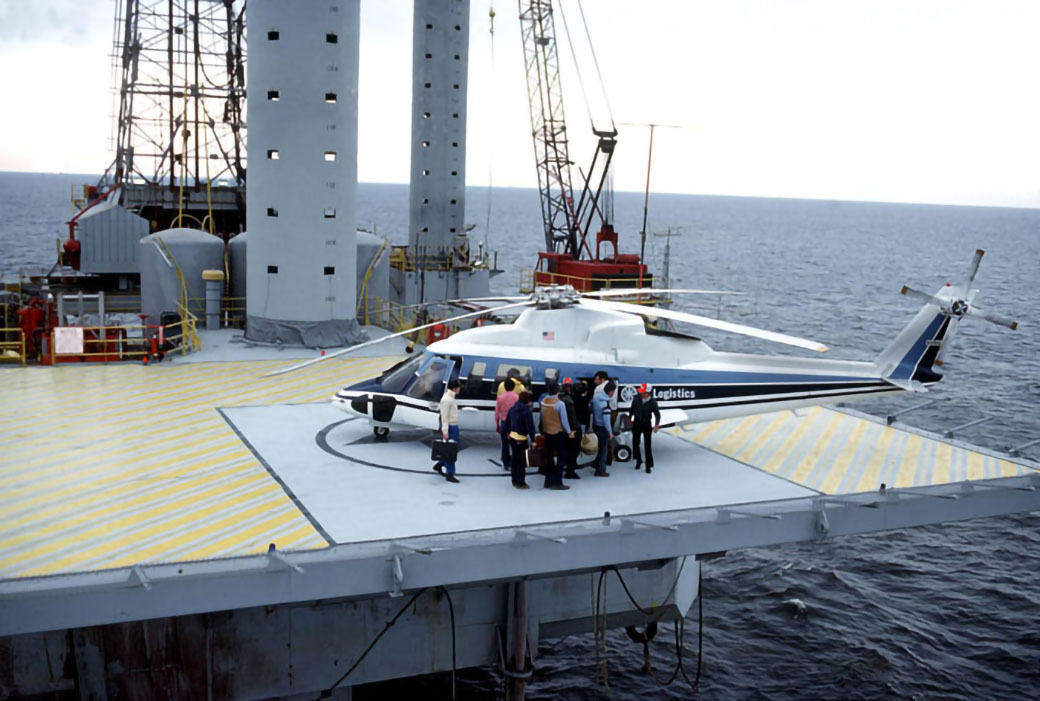
The first production variant was the S-76A. In 1982 this model set 12 world records for speed and time to climb in its weight class. A closed course 500 km (311 mi) speed record was set at 214.8 mph.
Several airlines operate the S-76A on scheduled services including Helijet International of Vancouver, British Columbia, Canada. Helijet International was recognized in February 2012 as the operator of the world’s highest flight time Sikorsky S-76® airframe an S-76A™ helicopter (Serial Number 760074) with 37,025 flight hours.
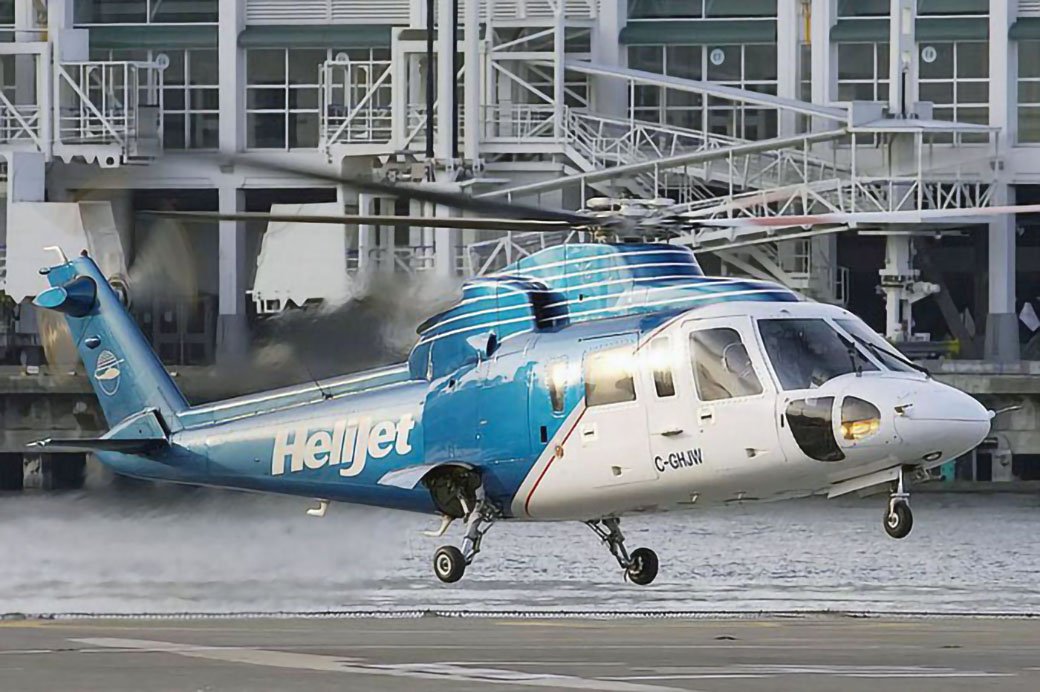
The Executive S-76 has become the “First Choice” for Fortunes 500 companies. The Queen’s Helicopter Flight which transports Queen Elizabeth II and the Royal Family has flown a Sikorsky S-76C+ since 1998. In 2009 a Sikorsky S-76C++ took over the duties
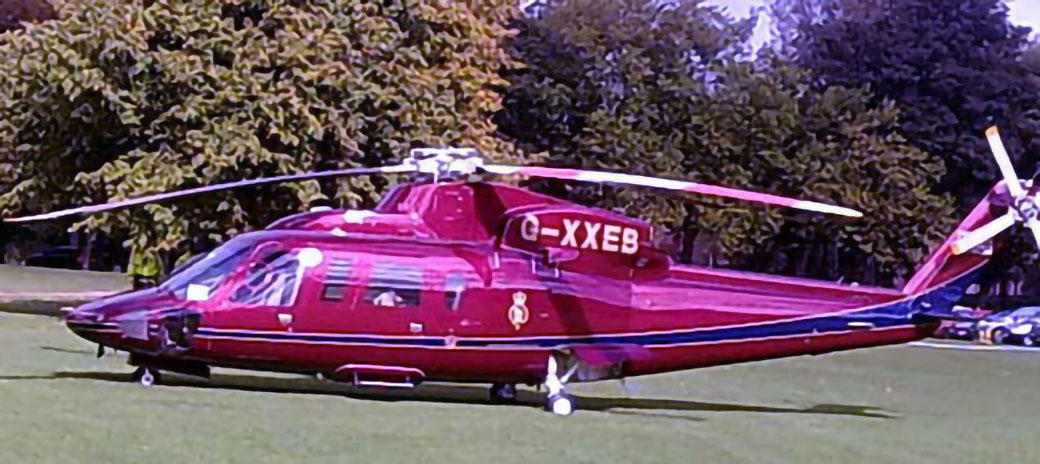
Although not in the original target market, Air Ambulance (EMS) has developed as an S-76 market based on its high dash speed, long range, and room for 2 patients plus equipment which are not available in the EMS competition.
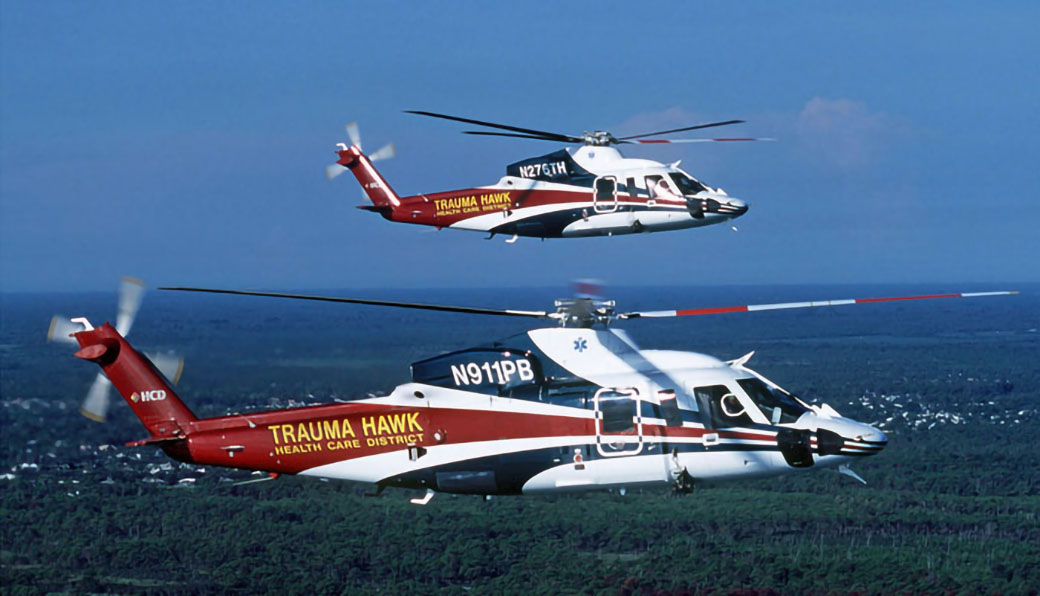
S-76 Development Timeline
Program Start
Public Introduction
Detailed Design Complete
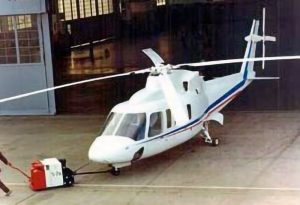
Prototype Rollout
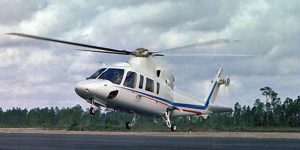
First Flight
FAA Certification Issued
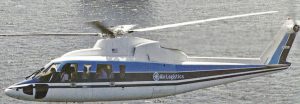
First Delivery
S-76A Introduced
S-76A+ Introduced
S-76A++ Introduced
S-76B Receives FAA Certification
S-76C Receives FAA Certification
S-76C+ Receives FAA Certification
S-76C++ Receives FAA Certification
Configuration Features
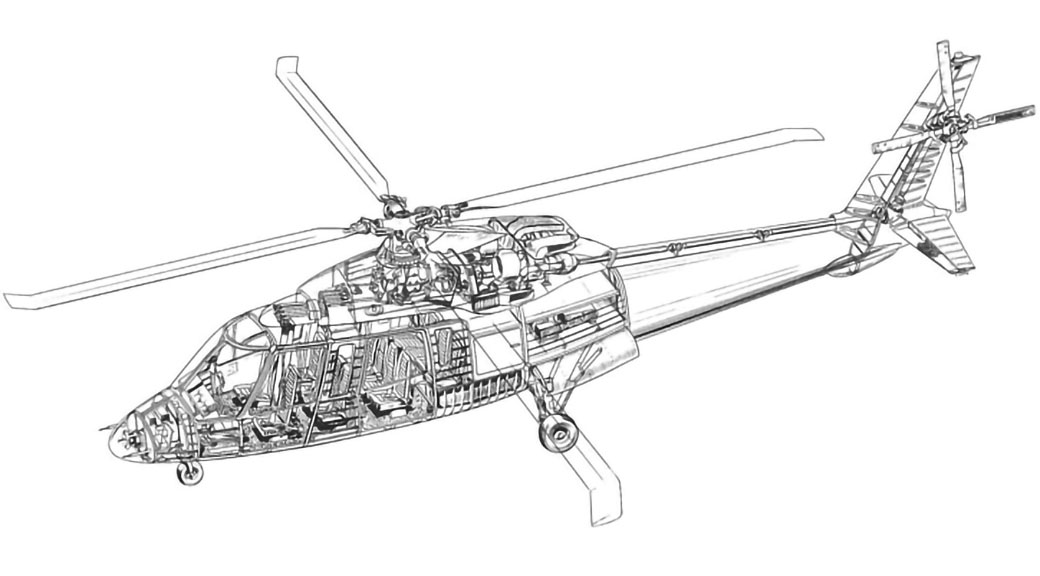
The S-76 helicopter was designed to serve the off-shore oil market and meet its requirements to carry 12 passengers and a crew of 2 on a 400 nautical mile radius mission with flotation equipment and operate IFR Category A. In order to achieve the design goals, the S-76 employed technologies developed for the UH-60 BLACK HAWK helicopter. Among the features are: titanium and composite main rotor blades, a bearingless composite tail rotor, bifilar vibration absorbers, and a simplified main rotor transmission.
The main rotor blades incorporate composite materials including a hollow titanium spar that is plasma arc welded and hot formed to its oval shape, a fiberglass cover, a redundant graphite root end, a Kevlar tip cap and Nomex honeycomb in the trailing edge. The main rotor blades use an SC1095 airfoil and have a non-linear twist to load the blades evenly in a hover. Tip caps are swept to reduce noise and vibration.
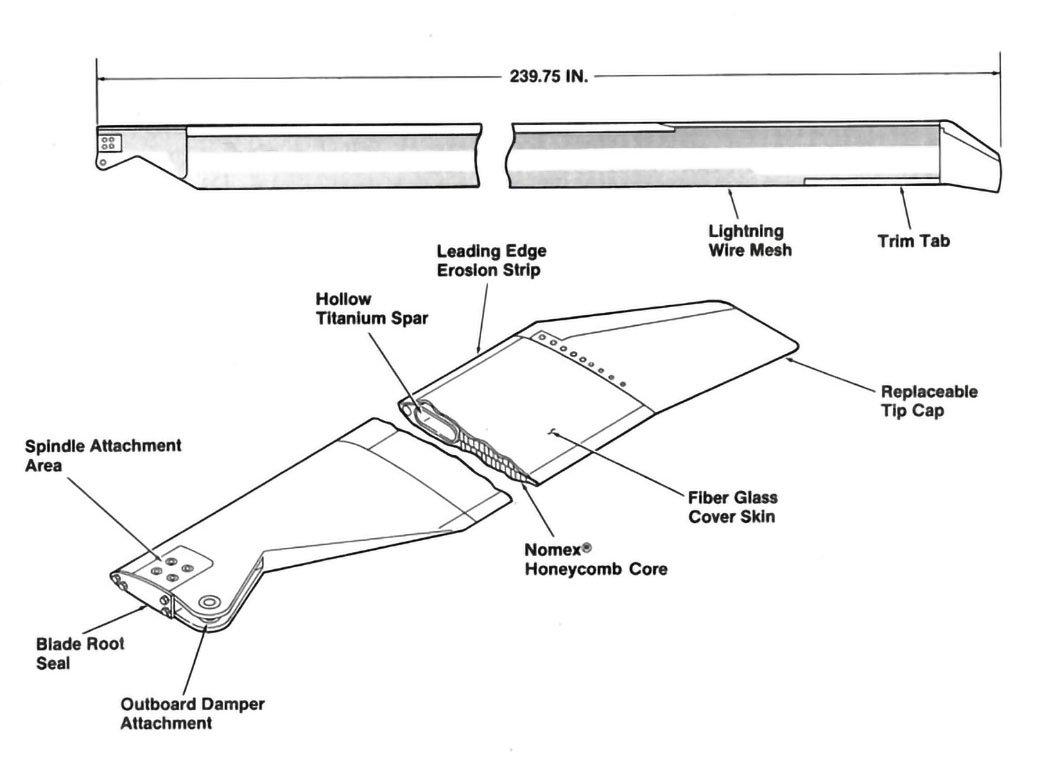
Ride quality in the S-76 was enhanced by a pitch-cone coupling to a maximum of 17 degrees. The cyclical feathering motion, usually known by the mathematical shorthand “Delta-3”, functions to wash out blade pitch during blade flapping. In other words, when the blade flaps up as it would in turbulence, Delta-3 mechanically washers out some of the pitch angle to prevent tip stall and soften the ride. Delta-3 was incorporated in the S-76 by a phase shifter incorporated in a complex mixer unit.
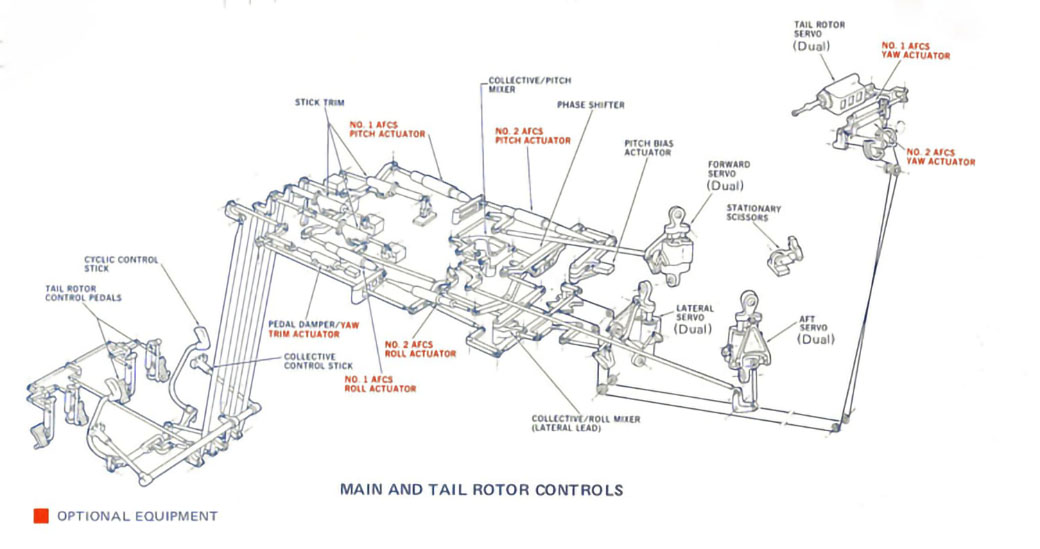
The composite bearingless tail rotor principle structural element is the cross beam spar. The cross beam tail rotor is designed to take advantage of the special capabilities of unidirectional graphite composites. The tail rotor consists two assemblies each of which provide two blades for the four bladed tail rotor. The spar which connects opposite blades is made of unidirectional graphite and is laid up in a rectangular cross sectional shape. The resultant beam is flexible in the flapwise and torsional direction but very stiff in the edgewise direction. An airfoil shape is bolted to each end of the cross beam to form one half of the tail rotor. Two of these assemblies are clamped at right angles to form the tail rotor. The resultant tail rotor is free of instabilities and requires no lubrication or maintenance.
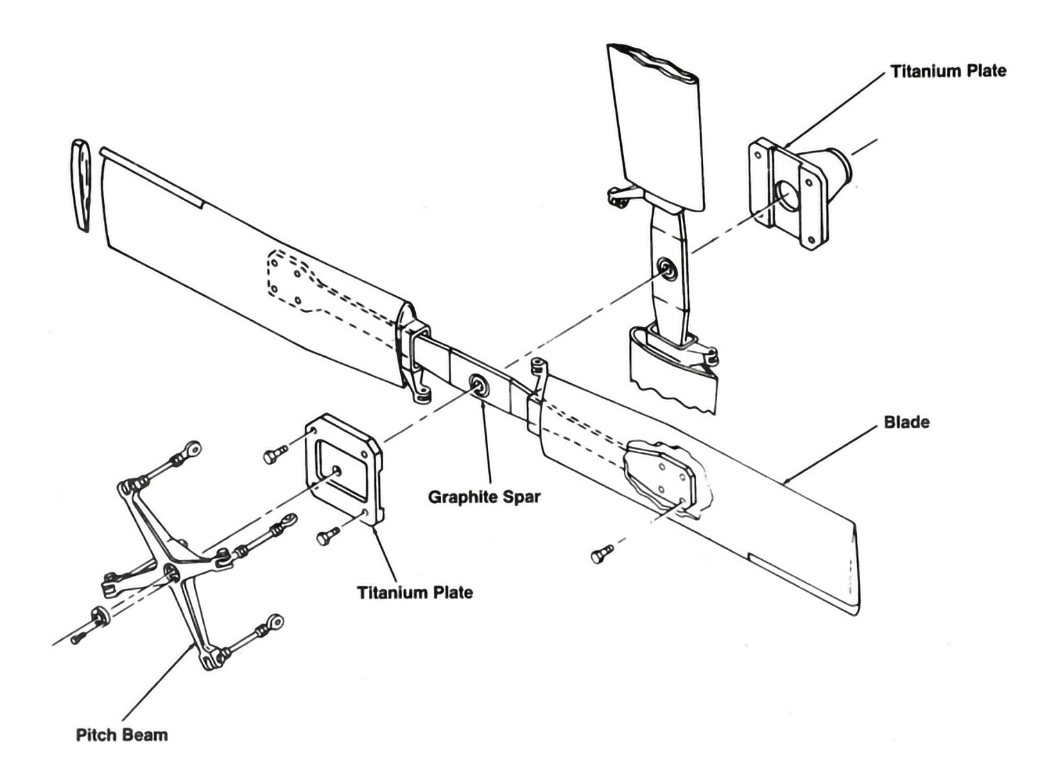
The Main Gearbox has as its final reduction a bull gear with two spur gear inputs. This is considerably simpler than the planetary gear system used in previous Sikorsky helicopter models Each engine has a separate power train all the way up to the bull gear through a single spur and a single bevel mesh. The tail takeoff is from the left engine power train. In case of a left engine failure the tail takeoff still drives through the right engine to the bull gear back through the bevel set to the tail take off. The freewheeling units are inside the first spur gear forward of each engine. Using the bull gearing system reduces the number of bearings and gears by a significant number over a conventional planetary gearing approach. This design results in a lower total cost and increased reliability.
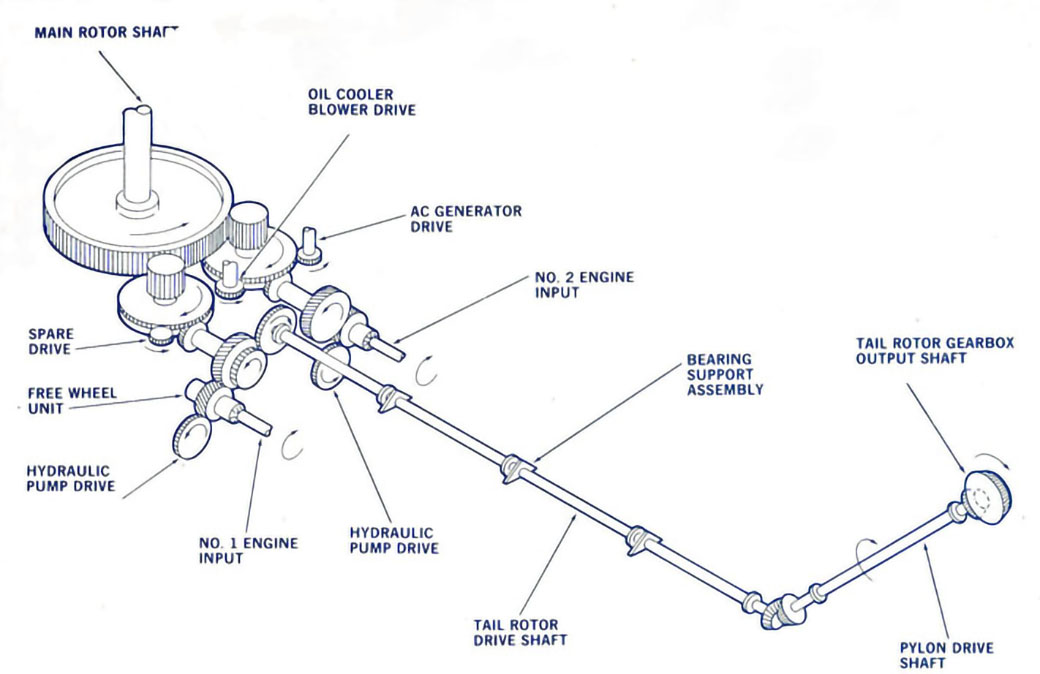
The main rotor hub is a single piece aluminum forging with elastomeric bearings and Bifilar vibration absorbers tuned to different frequencies to dampen vibrations at the source to reduce cabin noise and protect the airframe from vibration damage.
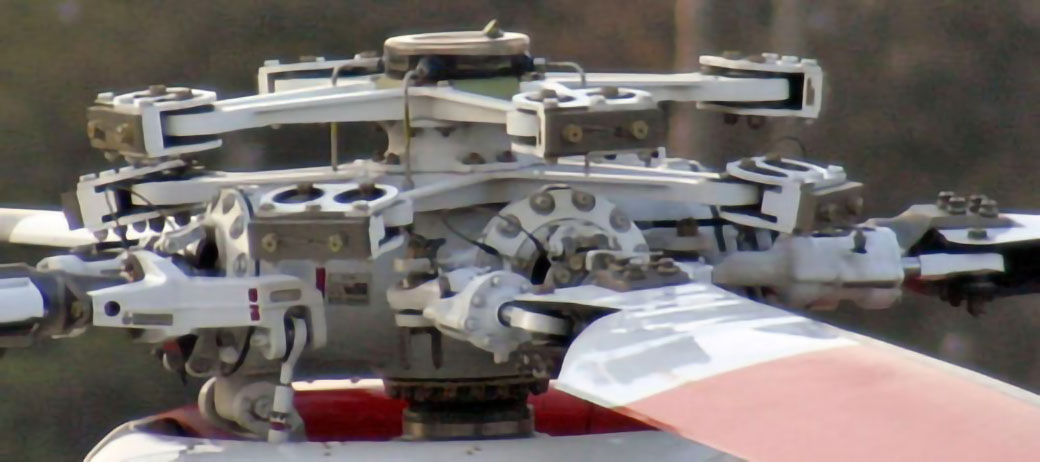
The S-76 fuselage is designed for low drag to improve efficiency. Flush rivets are used, a first for any Sikorsky helicopter. The S-76 was the first Sikorsky commercial helicopter to make extensive use of advanced composites. Kevlar is used for engine cowlings and fairings which is half the weight and twice the strength of fiberglass.
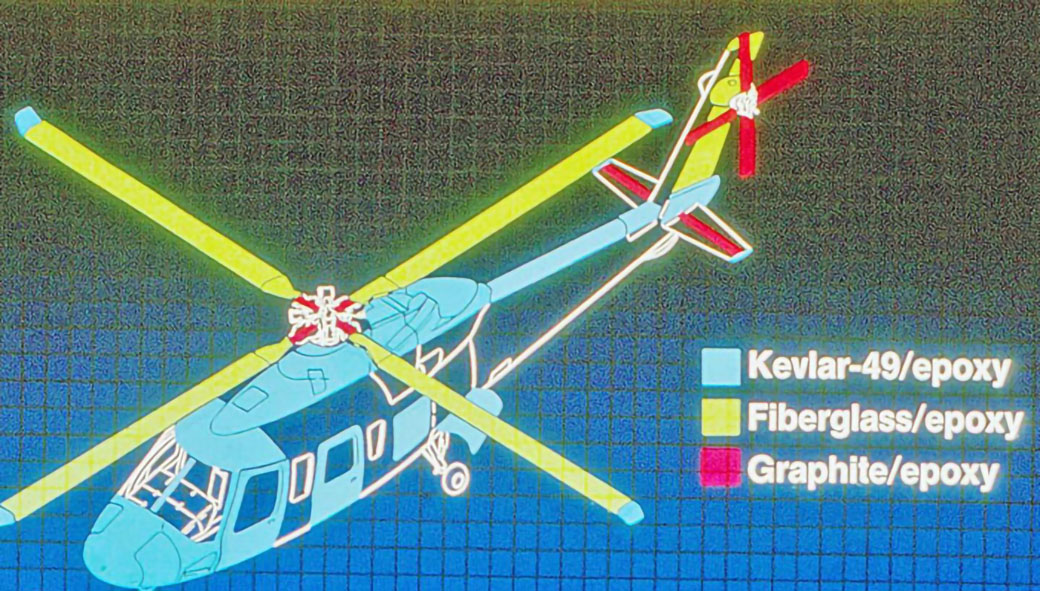
Model/1st Delivery | Year of First Delivery | Engines (Max. Continuous Power) | Improvements | Gross Weight | |
---|---|---|---|---|---|
S-76A | 1979 | Allison 250-C30 (557 shp) | 10,500 lbs | ||
S-76 Mark II | 1982 | Allison 250-C30S (557 shp) | 40 mods to improve reliability & maintainability. Mods were available as Kits and most S-76As were brought up to the MK II standard. 2 Year, 1,000 hour Warranty added. | 10,500 lbs | |
S-76A+ | 1986 | Turbomeca Arriel 1S (701 shp) | Increased performance and engine reliability | 10,500 lbs | |
S-76A++ | 1987 | Turbomeca Arriel 1S1 (725 shp) | Increased engine power | 10,500 lbs | |
S-76B | 1985 | P& W Canada PT6B-36A (887 shp) | 48% increase in takeoff power. 50% increase in useful load under hot and high conditions. Transmission strengthened and airframe strengthened and lengthened | 11,700 lbs | |
S-76C | 1991 | Turbomeca Arriel 2S (730 shp) | Incorporated the S-76B strengthened transmission and airframe. Arriel engines used for weight savings and fuel economy | 11,700 lbs | |
S-76C+ | 1996 | Turbomeca Arriel 2S1 (787 shp) | FADEC Engine Controls. QUIETZONE® main gearbox | 11,700 lbs | |
S-76C++ | 2006 | Turbomeca Arriel 2S2 (832 shp) | FADEC Engine Controls & Inlet Barrier Filters. QUIETZONE® main gearbox | 11,700 lbs | |
S-76D | P& W Canada PW210S (1077 shp) | 11,700 lbs |
General Arrangement Drawing

General Characteristics and Performance
Performance Standard Day At Sea Level | S-76C++ |
---|---|
Maximum Gross Weight | 11,700 lbs / 5,300 kg |
Maximum Cruise Speed | 155 kts / 287 kph |
Maximum Range Cruise Speed | 137 kts / 254 kph |
Maximum Range – No Reserve | 411 nm / 762 km |
HIGE (Hover In Ground Effect) | 7,050 ft / 2,149 m |
HOGE (Hover In Ground Effect) 11,650 lbs. ,Sea Level | 3,300 ft / 1,006 m |
OEI (One Engine Inoperative) Service ceiling | 4,900 ft / 1,493 m |
AEO (All Engines Operating) Service Ceiling | 13,800 ft / 4,206 m |
Weights | S-76++ | |
---|---|---|
Empty Weight | 7,007 lbs. | |
Maximum Gross Weight | 11,700 lbs. | |
External Loads Gross Weight | 11,700 lbs. | |
External Loads Gross Hook Limit | 3,300 lbs. |
General Data | S-76C++ |
---|---|
Crew seating capacity | IFR 2 Pilots VFR 1 Pilot |
Seating capacity, airline-style seating | IFR 12 passengers VFR 13 passengers |
Baggage compartment volume | 42 cu ft / 1.19 cu m |
Fuel capacity (internal, standard) | 272 US gal / 1030 L |
Aircraft Dimensions | S-76C++ |
---|---|
Main rotor diameter (blade tip circle) | 44’ 0” / 13.41 m |
Tail rotor diameter (blade tip circle) | 8′ 0″ / 3.35 m |
Fuselage length | 44′ 1″ / 13.44 m |
Fuselage width | 7’ 0″ / 2.13 m |
Length over-all (including rotors) | 52′ 6″ / 16.0 m |
Height over-all | 14’ 6” / 4.41m |
Width | 7′ 0″ / 2.13m |
Main landing gear tread | 8′ 0″ / 2.44 m |
Wheel base | 20′ 4″ / 6.20 m |
Passenger cabin length (with bulkhead) | 20′ 0″ / 6.10 m |
Passenger cabin width | 6′ 7″ / 2.01 m |
Passenger cabin height | 6′ 0″ / 1.83 m |
Production History
Model | Aircraft Produced |
---|---|
S-76A and S-76+ | 307 |
S-76B | 103 |
S-76C and S-76C+ | 191 |
S-76C++ | 213 |
S-76D | In Production |
Related Models: Military
AUH-76 Armed utility transport version, developed from the S-76 Mk. II. Four were sold to the Philippine Air Force
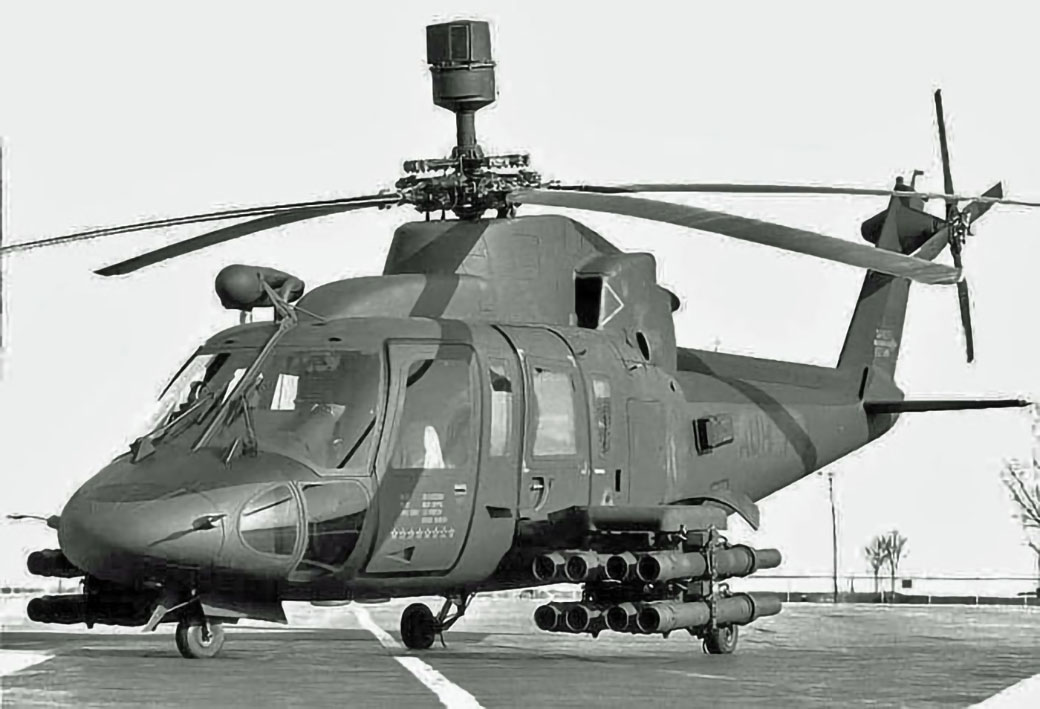
H-76 Eagle Military version of the S-76B. Designed to provide a lower cost alternative to the AH-64 Apache. One built.
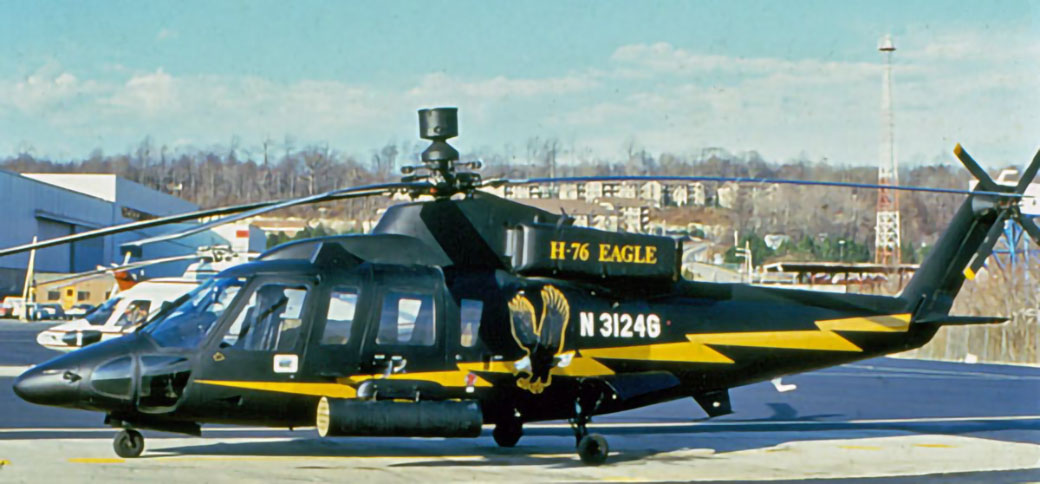
H-76N Planned naval version proposed to New Zealand
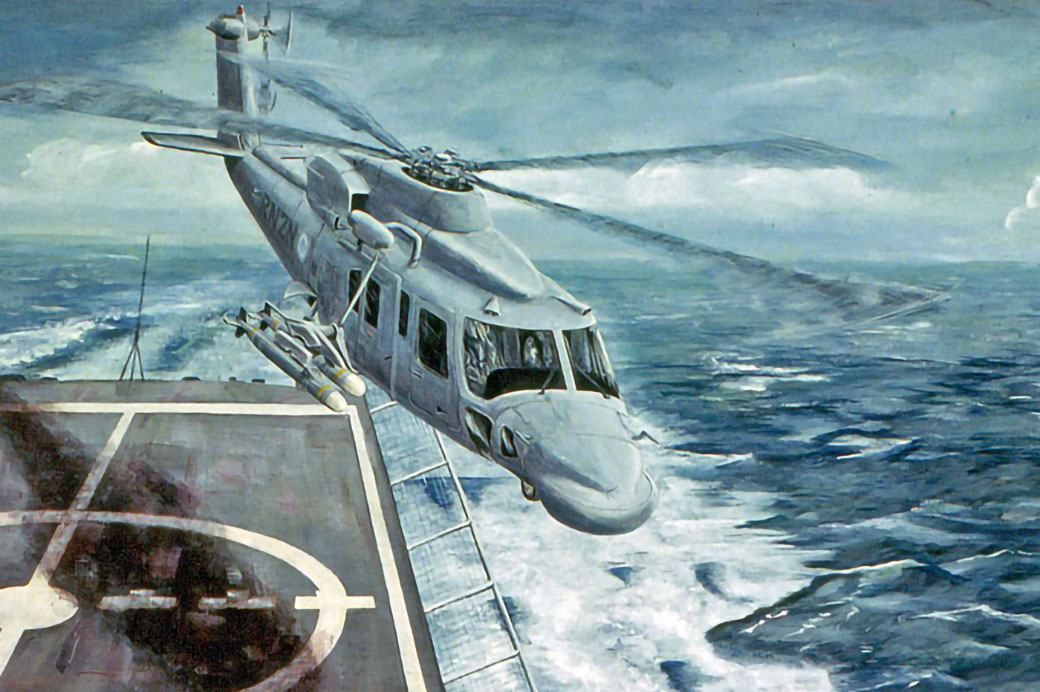
Related Models: Experimental
SHADOW (Sikorsky Helicopter Advance Demonstrator of Operator Workload) An S-76A with an extended pilot station added to the nose to develop a fly-by wire flight control system for the RAH-66 Comanche program. A safety pilot flew in the normal pilot position to take control of the helicopter if required.
SHADOW was used to test three and four axis side arm controllers. It also tested unique flight control software concepts such as velocity hold which allowed the pilot to release the stick and the helicopter would continue to fly at the set speed. This and other concepts tested were designed to minimize the pilot’s flying workload so he could concentrate on the mission requirements.
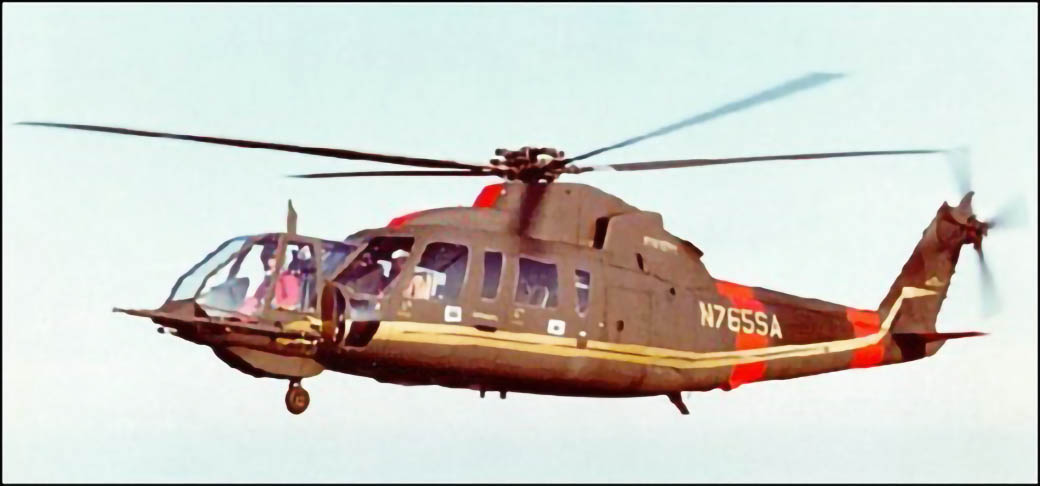
Fantail S-76B with a fan-in-fin tail rotor to test the configuration for the RAH-66 Comanche which required the ability to do a 180 degree turn in 6 seconds with a 45 knot crosswind under hot and high conditions. This led to a very powerful fan and the ability to fly sidewards at 70 mph.
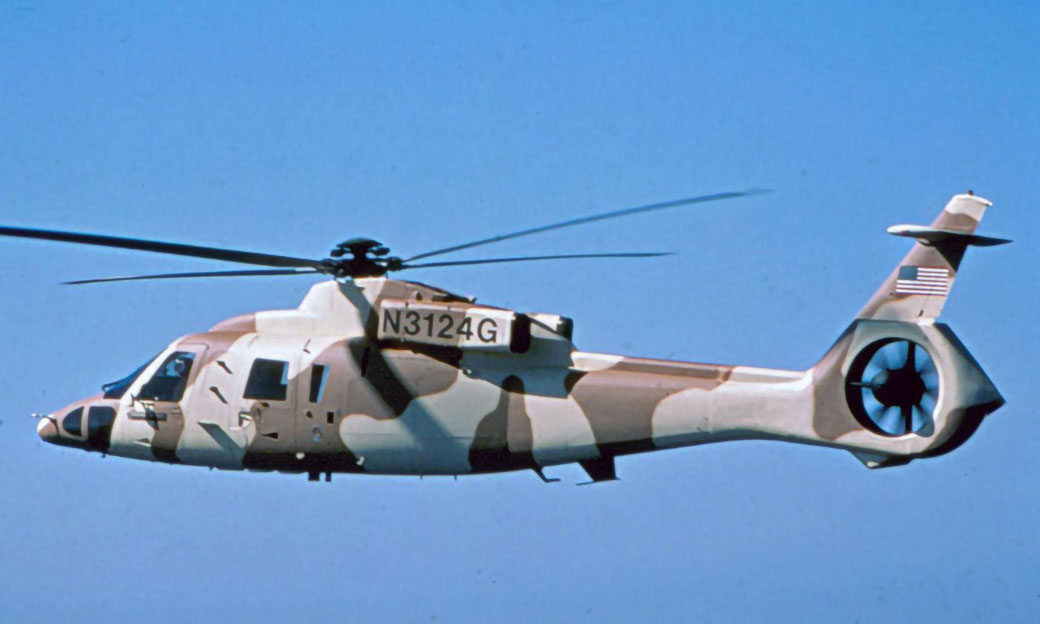
- by Vinny Devine
Related Articles
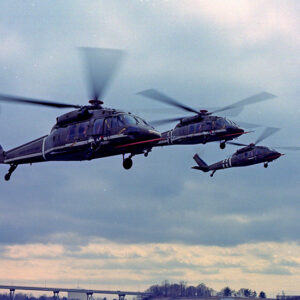
Bill Paul: Reflections on Sikorsky’s 100th Anniversary
Former Sikorsky President Bill Paul reflects on his career with Sikorsky, meeting Igor Sikorsky, and the Sikorsky Aircraft Company’s 100th anniversary.
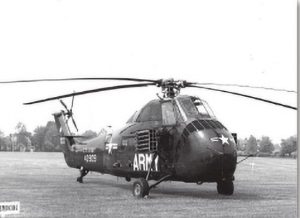
Evolution of the Armed Helicopter
Military users quickly understood the flexibility and fire-power of rotary wing platforms and ultimately evolved highly integrated weapons systems ready to protect themselves and others.
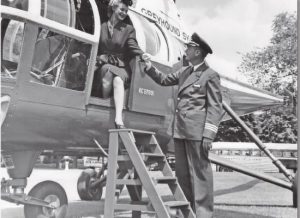
Sikorsky Helicopters in Airline Service
Early in the evolution of Sikorsky helicopters, Igor Sikorsky and his team envisioned scheduled passenger flights serving major cities.
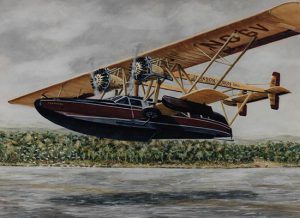
Sikorsky Aircraft Color Schemes
This issue of the newsletter illustrates some of the artistic variations in the exterior color schemes of aircraft delivered during Igor Sikorsky’s three careers.
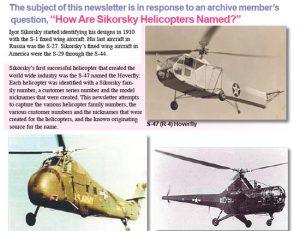
How Sikorsky Helicopters Are Named
The subject of this newsletter is in response to an archive member’s question, “How Are Sikorsky Helicopters Named?”
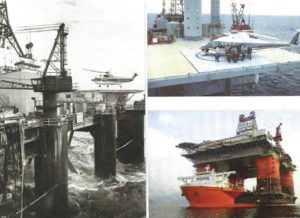
Revolutionizing Transportation in the 1950s
Igor Sikorsky’s large cabin single main rotor helicopters revolutionized the energy, health and other industry’s transportation requirements during the 1950s.
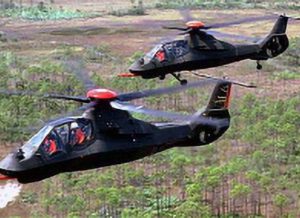
Sikorsky Aircraft in the 1990s
During the 1990s Sikorsky Aircraft produced the H-60 Hawks and the S-76 while developing the Boeing Sikorsky RAH-66 Comanche and the S-92 helicopters.
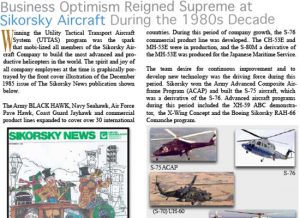
Sikorsky Aircraft in the 1980s
Business optimism reigned supreme at Sikorsky Aircraft during the 1980s decade.
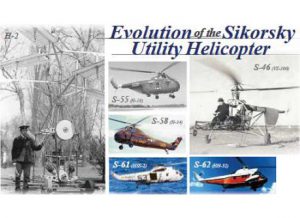
Evolution of the Sikorsky Utility Helicopter
This newsletter focuses on the evolution of Sikorsky utility helicopters.