Sikorsky Product History
Sikorsky X-WING
Background
The X-Wing is one of a number of concepts proposed to combine the hovering capabilities of the helicopter with the speed potential of fixed wing aircraft. It uses a large-diameter four-bladed stiff rotor system that can be stopped in flight to become an “X” wing. It has the promise of breaking the trend of VTOL aircraft where higher speed requires higher hovering disc loadings (weight of the aircraft divided by the area of the rotor disc, expressed as lbs./sq.ft.) Additionally it can achieve fixed wing flight without the need for a separate wing, promising a lower weight empty fraction (empty weight/gross weight)over those concepts that need both a rotor system and a wing. Because of its low hovering disc loading plus the power to fly at high subsonic speeds, a two-engined X-wing aircraft could hover and fly a good portion of its flight envelope on only one engine.
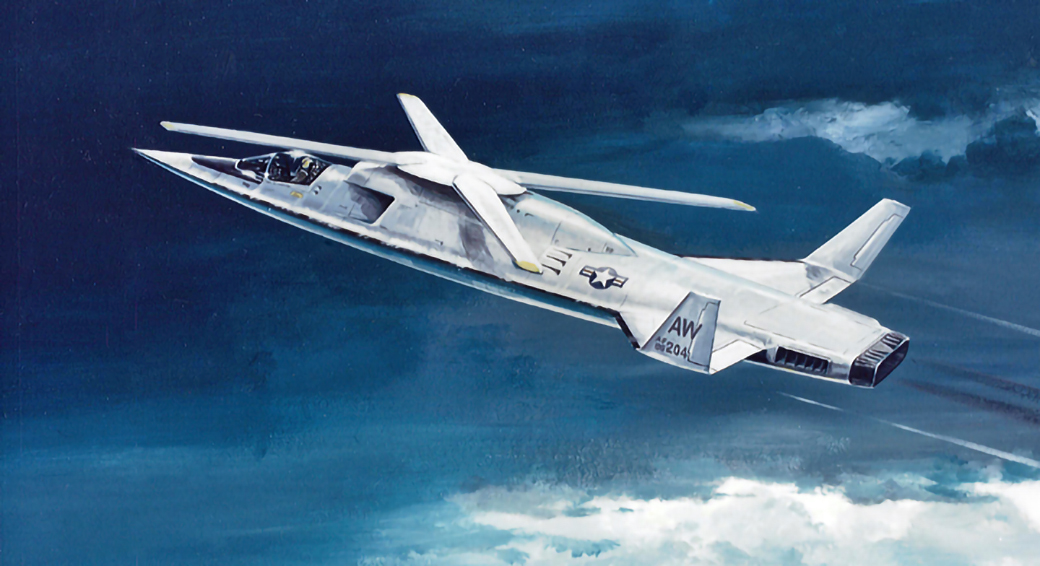
The X-Wing concept is based on the initial work of Professor Ian Cheeseman of the University of Southhampton, England, and his experiments with what some called a “Flying Stovepipe”. Dr. Cheesman employed the Coanda principal to create and then modulate the lift on a cylindrical rotor blade. The Coanda principle is that if air is blown tangentially over a surface it will adhere and follow the surface until the curvature gets too great and it detaches. Thus it can be used as a virtual flap on an airfoil. He believed that such a rotor could be stopped and started in flight if used on a winged vehicle, and employed only for takeoff and landing. The rotor would then be stopped and stowed for cruise efficiency.
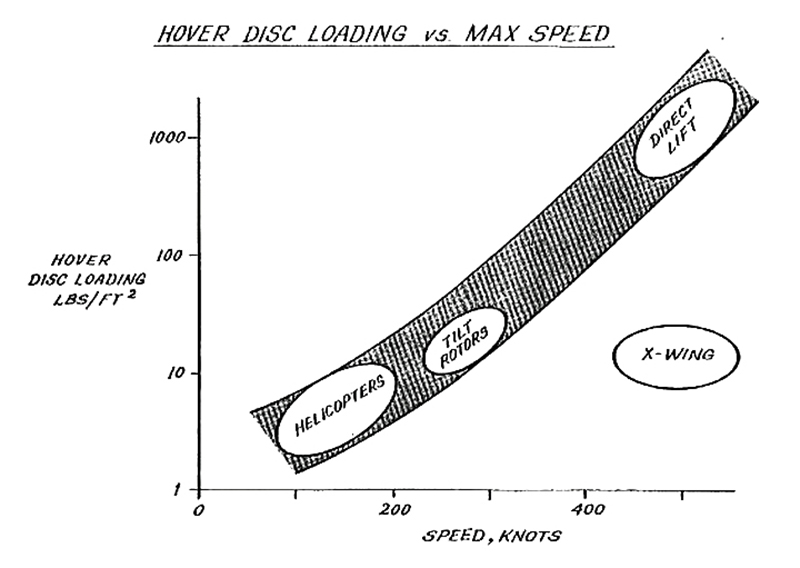
Engineers at the U.S. Navy’s David W. Taylor Naval Ship Research and Development Center (DTNSRDC) extended Professor Cheesman’s idea of lift control on a cylinder using circulation control by blowing tangential to a rounded trailing edge of a streamlined shape similar to a conventional airfoil. This then evolved into the X-Wing concept where circulation control airfoils could produce lift in either direction and allow the rotor/wing to maintain lift and control while starting and stopping rotation. In 1976 DARPA (the Defense Advanced Research Projects Agency) joined the Navy in X-Wing development.
Quoting the winter 1982 AIAA Student Journal in an article on the X-Wing by Robert M. Williams, DARPA Program Manager:
“The focal point for all of the experimental and analytical work during 1976-1979 was a large-scale flight worthy rotor and control system demonstration. A small elite team of Lockheed engineers was formed which initially performed an aircraft preliminary design and analysis of a small 3000 pound flight test vehicle with a 25 foot diameter rotor/wing. This design was created in order to place the critical rotor/hub/control system development in proper perspective. Using available small turboshaft engines, a flight envelope of approximately Mach 0.70 at 20,000 feet would have been expected. Following the feasibility activity, a flight worthy rotor system design and fabrication was initiated in mid-1977, with whirl tower testing commencing in late 1978. In the spring of 1979, the test module entered the NASA Ames 40 x 80 wind tunnel for seven weeks of exhaustive testing. During this period the system was tested in helicopter, fixed-wing, and conversion flight modes with the moment feedback control system in open- and closed-loop operation. More than 30 automatic rotor stops and starts were conducted, most at 180 knots, as part of the test program”
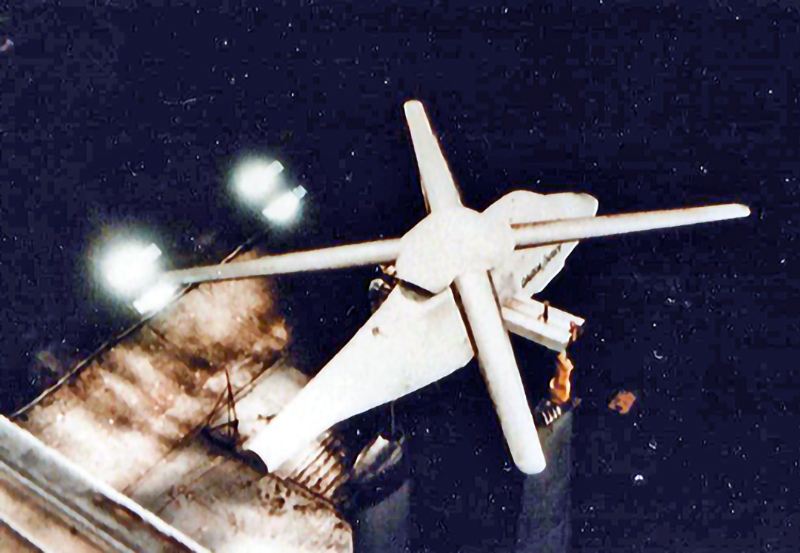
From the success of these tests, DARPA and the Navy, with additional support from NASA, decided to progress to a larger-scale flight test of the X-Wing rotor/wing. Sikorsky was contracted in 1982 for this development, with the idea of testing the rotor/wing on the recently delivered NASA/Army/Sikorsky S-72 RSRA (Rotor Systems Research Aircraft). The S-72 RSRA was a unique aircraft designed solely for testing advanced helicopter rotors. It had a variable incidence wing which could offload or overload the rotor’s lifting requirements. It had auxiliary propulsion and drag brakes to offload or overload the rotor’s horizontal thrust requirements. It thus would permit initial rotor/wing stopping and starting tests to be done in an orderly build-up fashion, without requiring the rotor to support its full design lift during initial conversions.
The X-wing was perhaps the most technically challenging concept Sikorsky had ever worked on. The rotor blades have to carry lift without the conventional helicopter’s use of centrifugal force for blade stiffening. The blades also have to be extremely stiff since two of them become forward-swept wings in the stopped rotor flight mode. The blades have to be “double-ended” since the blades on the retreating side of the rotor disc must fly “backwards” in stopped rotor flight. By using the Coanda effect to control blade lift, the helicopter’s conventional mechanical swashplate is replaced with a valving system in the pneumatic lines feeding air to the rotor blades. The starting and stopping sequence requires complex high-frequency manipulation of the circulation control valving system to provide controllable forces and moments during the conversion process. This requires the latest in the state-of-the-art in computation capability to control the process.
Other technical challenges included the design of large compressor to provide the circulation control air, and a high energy clutch and a brake to start and stop the rotor. Hub moment feedback was required to control the rotor in conversion. This was truly a “high-risk/high-payoff” program. Both the technical challenges and achievement of the full aircraft potential were major steps in the state-of-the-art.
Two design teams were established at Sikorsky. The first concentrated on developing the X-Wing rotor/wing systems as they would be applied to a demonstrator aircraft. The second worked on how to test these systems on the RSRA. Much detailed work was required on all the disciplines involved. A detailed 10 foot diameter wind tunnel model was developed to optimize the design. Testing with this model began in December, 1985 at Sikorsky. In June, 1986 it was tested in the United Technologies large-scale wind tunnel for forward flight tests prior to the actual RSRA flight test.
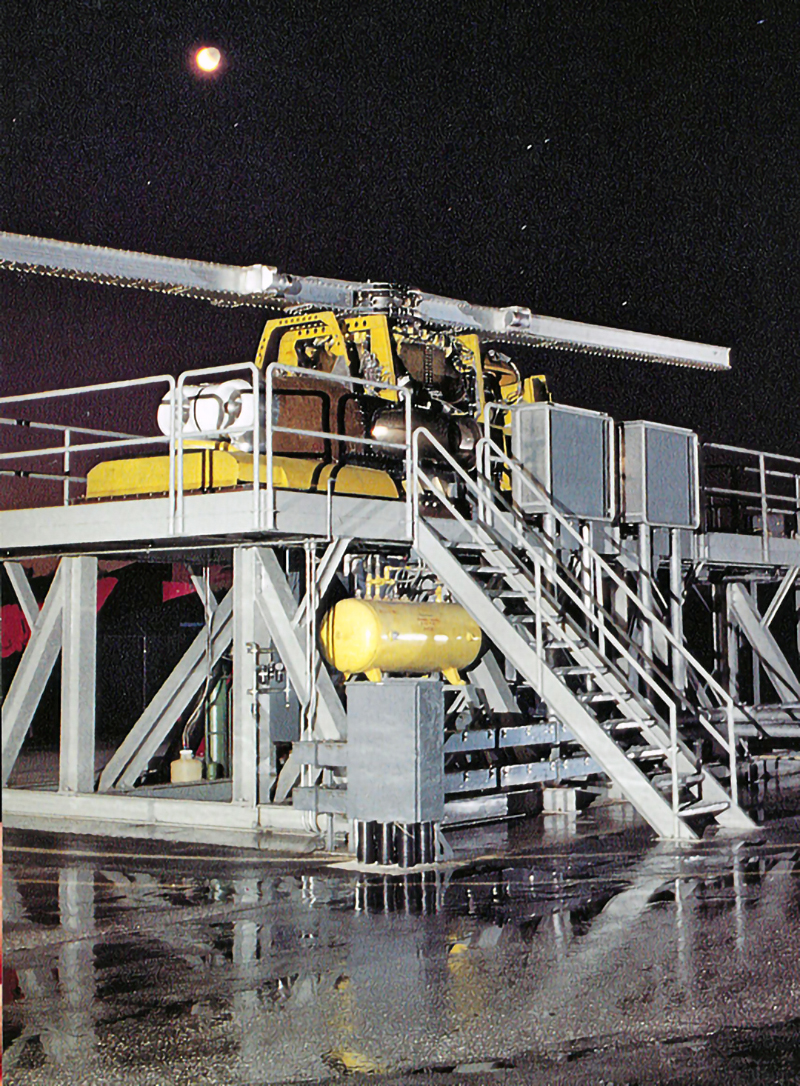
The entire X-Wing dynamic system was fabricated and tested on a Propulsion System Test Bed (PSTB) at Sikorsky’s West Palm Beach Florida test facility. Initial tests used dummy blades for development of the pnuemodynamic system from the compressor inlet to the blade root. Then the blades were installed for a full system test.
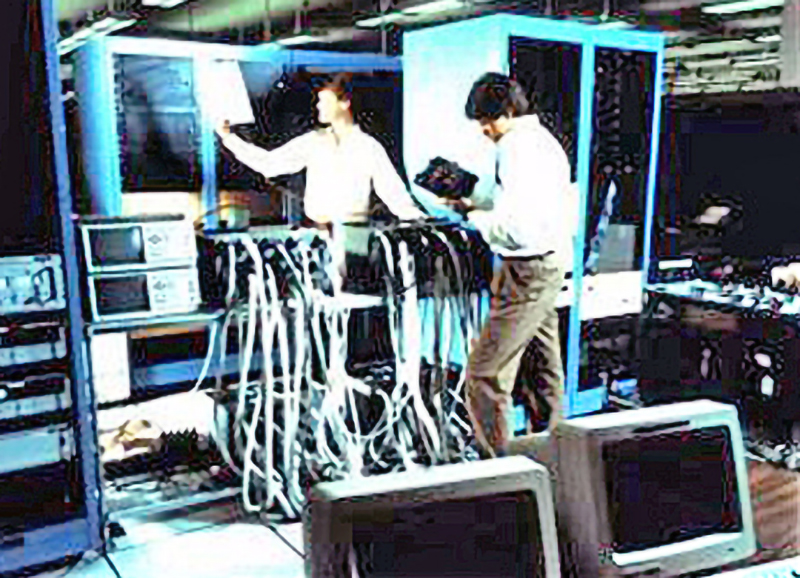
A Vehicle Management System Laboratory (VMSL) was created to develop the Vehicle Management System (expanded flight control system) prior to its use on the aircraft. The four computers were tied to a full set of aircraft sensors, hydraulics, electric power and actuation components, as well as a fixed-base cockpit. All the aircraft instrumentation was duplicated. An additional computer facility provided a simulation of the RSRA/X-Wing vehicle. Hundreds of operational hours were accumulated on the system prior to the start of the flight test program.
This VMSL became the prototype for all subsequent Sikorsky flight control system integration laboratories.
All of this came together on the RSRA test aircraft. The roll-out of the RSRA/X-wing occurred on August 19, 1986.
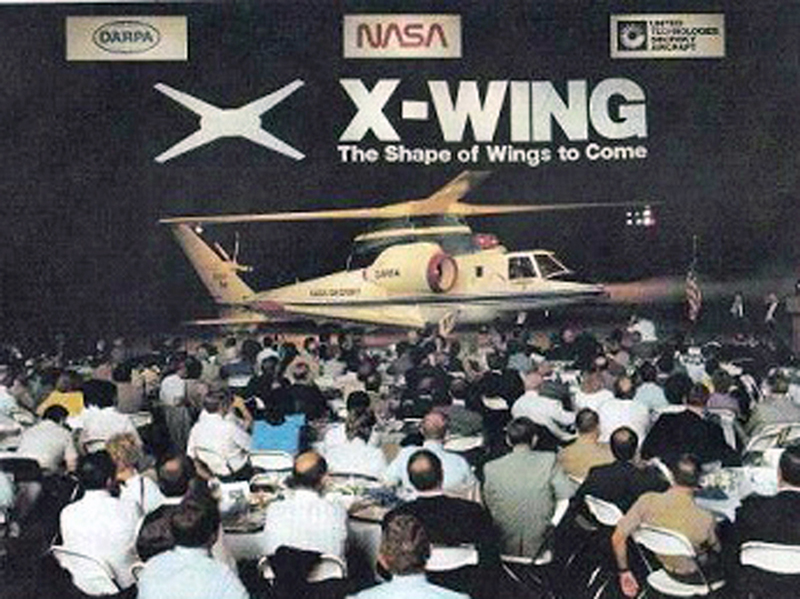
In September 1986 the aircraft was transported, via NASA’s Super Guppy KC-97 cargo aircraft, to NASA’s Dryden Flight Test Research Facility at Edwards Air Force Base in California.
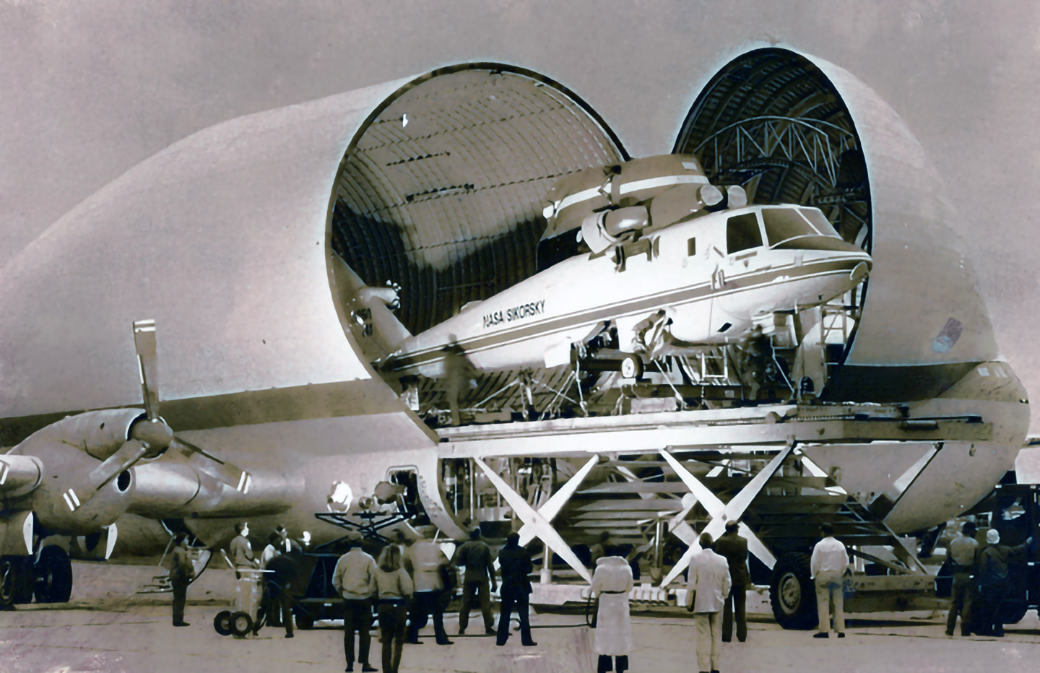
The flight test program was envisioned as a gradual buildup of the envelope. After taxi tests, the aircraft was flown without the X-Wing blades installed to establish baseline date.
RSRA was designed to fly new rotors when they were not producing lift, and to return to base in an emergency after the rotor blades had been severed from the rotor head. Thus it could fly as a fixed wing airplane without a rotor. When this test occurred it was a special event for the Sikorsky team. Igor Sikorsky spent his early career producing fixed-wing aircraft, including the large flying boats in the 1930s. But a new Sikorsky-designed fixed-wing aircraft had not flown in almost a half of a century
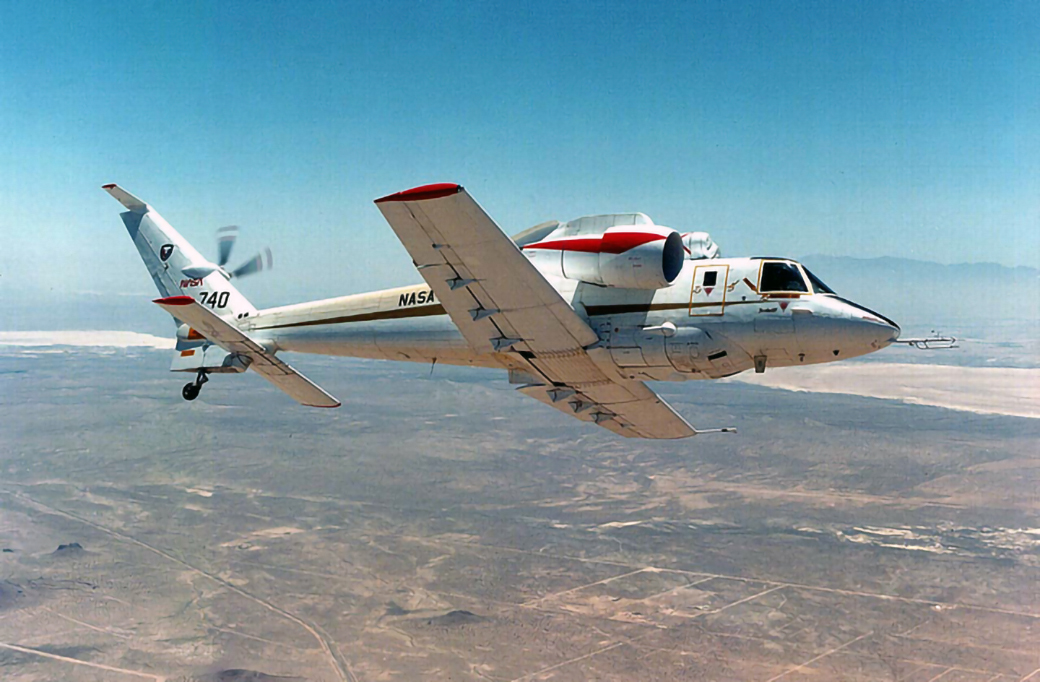
The plan was to then fly it first with two rotor blades, followed by four blades, with the rotors stopped. By mid-1987 the RSRA was scheduled to fly with the rotor/wing turning at full speed, and by year’s end the rotor/wing was to be stopped and started in flight.
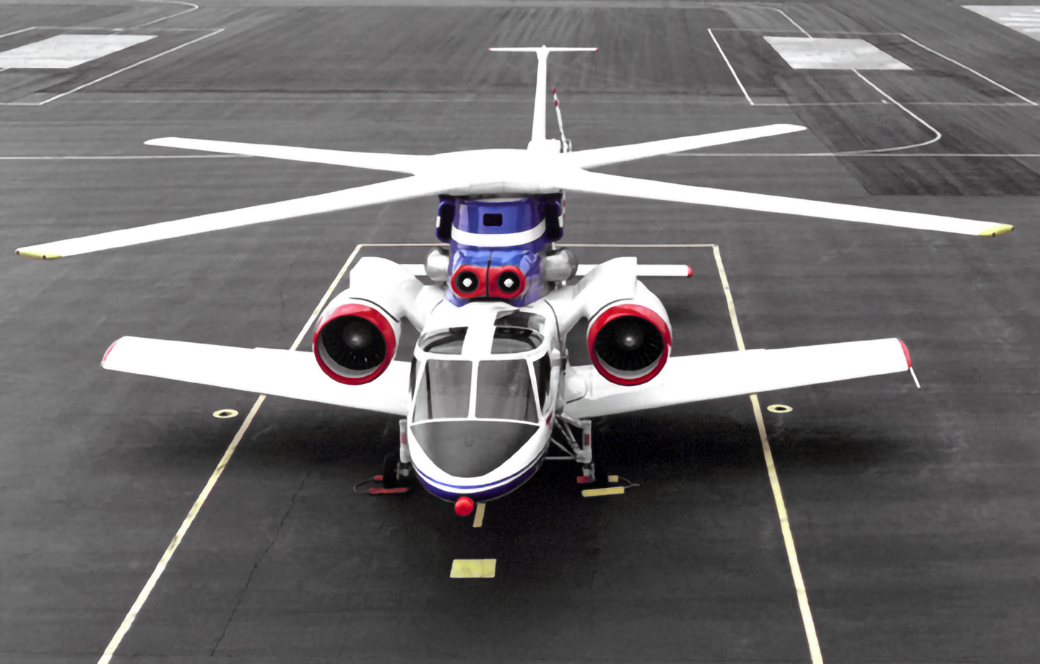
But, that was not to be. In 1987 the Government had funding issues and higher priorities, and decided to terminate the contract. The program was terminated due to this lack of funding rather than for any technical issues.
Configuration Features
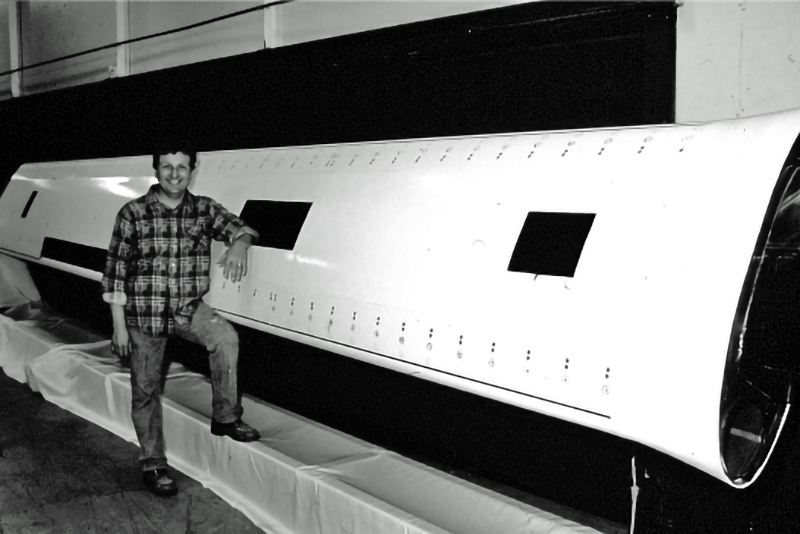
had previously produced.
The design and fabrication of the rotor/wing was the most difficult structural challenge. The blades could not rely on centrifugal stiffening like a conventional helicopter since they had to operate when the rotor was stopped. In addition, they had to be unusually stiff since when operating as an “X” wing two of the blades were swept forward at 45º. Composites were used to provide this extreme stiffness at an acceptable weight.
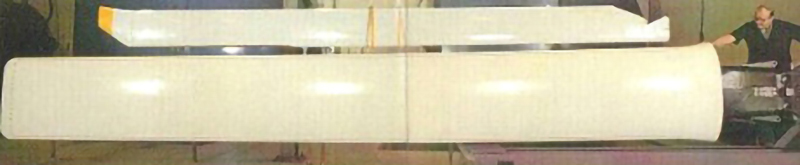
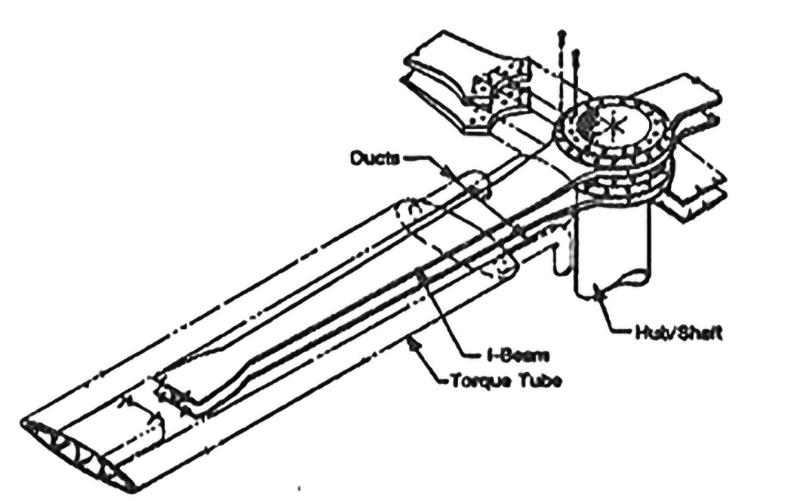
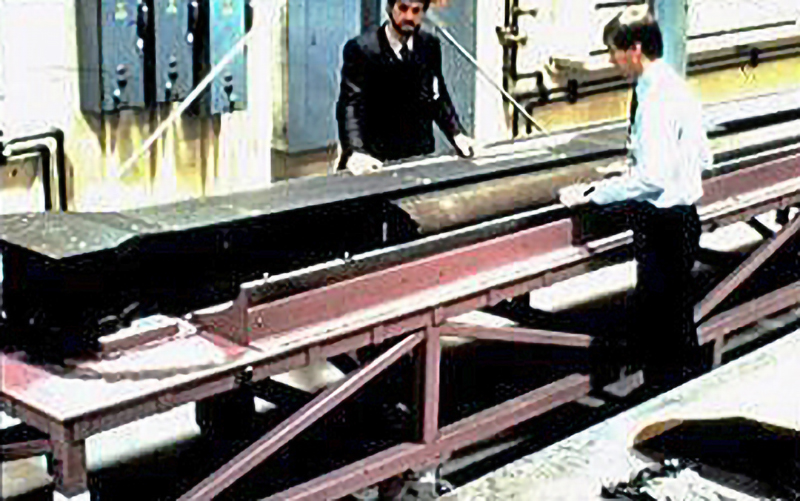
The blade manufacturing and tooling challenges were unprecedented in the rotary wing field and involved development of a unique curing process for the very thick composite components. New processes had to be developed to characterize the material, define the allowable void size and establish a quality control procedure.
One of the test features of the RSRA was the ability to pyrotechnically sever the rotor blades in case of an emergency, and to return to base as a fixed wing aircraft. It was desired to keep this feature for X-Wing testing. Developing this system for the very thick composite flexbeams of the X-Wing became another large development project and a great achievement for the team.
The airfoils were double-ended, with rounded leading/trailing edges so that they could produce lift in either direction. Circulation control was used to develop and modulate lift by blowing air out slots above the trailing edges which would attach to the surface and create virtual flaps. In the helicopter mode this provided the cyclic pitch, and had the additional advantage of being able to provide higher harmonic pitch which was required to control the rotor during the stopping and starting sequences. No mechanical cyclic control was needed, although a mechanical collective pitch mechanism was used similar to that used on conventional helicopters.
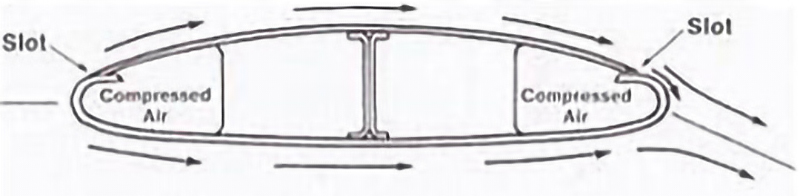
The following illustration shows the need for both leading and trailing edge blowing. In rotary wing mode, air is blown out the trailing edges of the blades. In the fixed wing mode, two of the blades are now flying “backwards” with blowing now required on what was the leading edge. During conversion the aerodynamics get much more complicated, with circulation control blowing required out of both the leading and trailing edges at the same time.
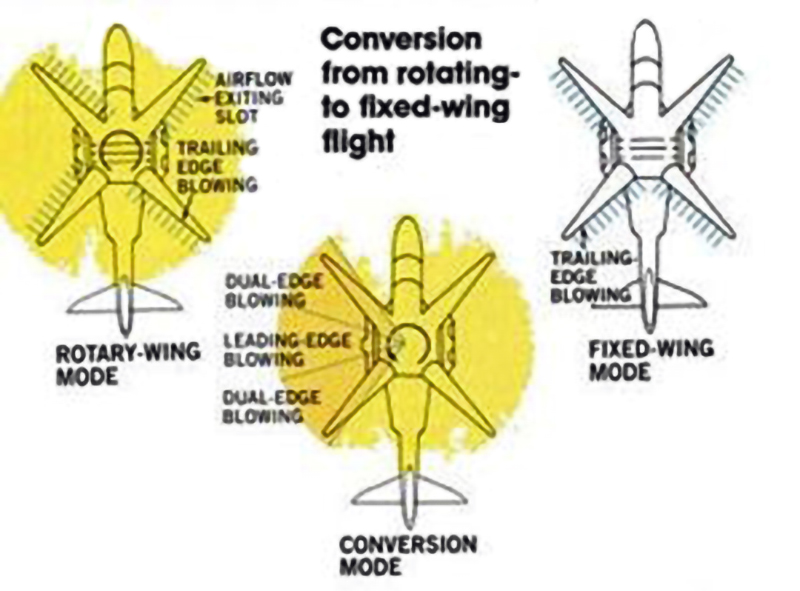
To provide the air for the circulation control system a two-stage axial compressor was used driven off the main gearbox. This unique compressor was developed by Pratt & Whitney in Florida. It fed air to a plenum mounted below the rotor concentric with the rotor shaft. This was a pneumatic swashplate, with the stationary element collecting air from the compressor, valves to control the flow, and a rotating element which passed the air out to the blades.
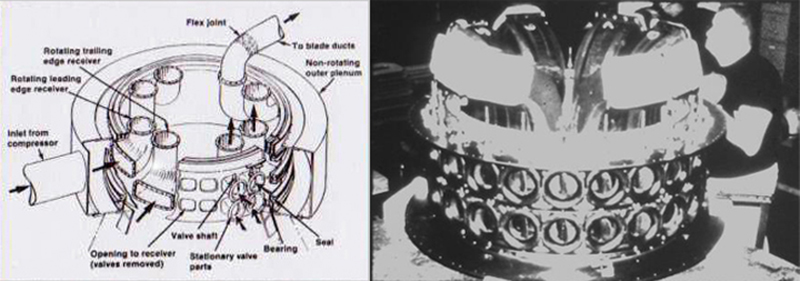
Both a high energy clutch and brake were provided for the rotor starting and stopping operations. The clutch was developed by Allison. The clutch concept became the basis of the clutch design eventually used to manage the lift fan on the Joint Strike Fighter, the F-35.
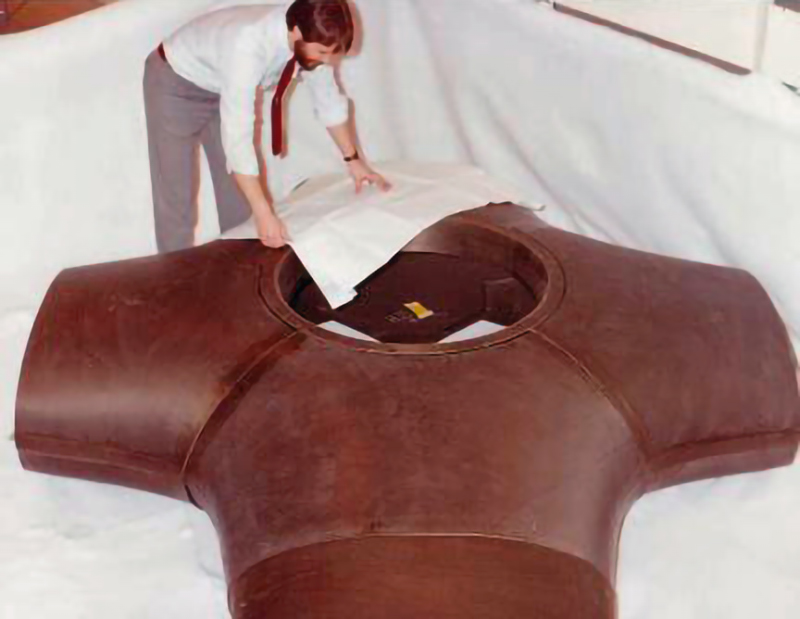
A full authority, quad redundant, digital fly-by-wire vehicle management system was used to control the blade aerodynamics up to the fourth harmonic with rapid response characteristics. This was done by controlling the pneumatic control valves in the plenum as well as the mechanical collective pitch change mechanism and the compressor. During the conversion process it also controlled the clutch, the brake, and the positioning index system.
The revolutionary flight control computer was developed by The Hamilton Standard Division of UTC. At the time it was the most sophisticated system of its kind other than the space shuttle.
For the prototype aircraft a convertible engine was planned which could provide both shaft power for the rotor and compressor and thrust for high speed flight, and modulate between the two in a controlled fashion. A cross section of such an engine is shown below. In this design, variable inlet guide vanes control the mix between shaft power and thrust.
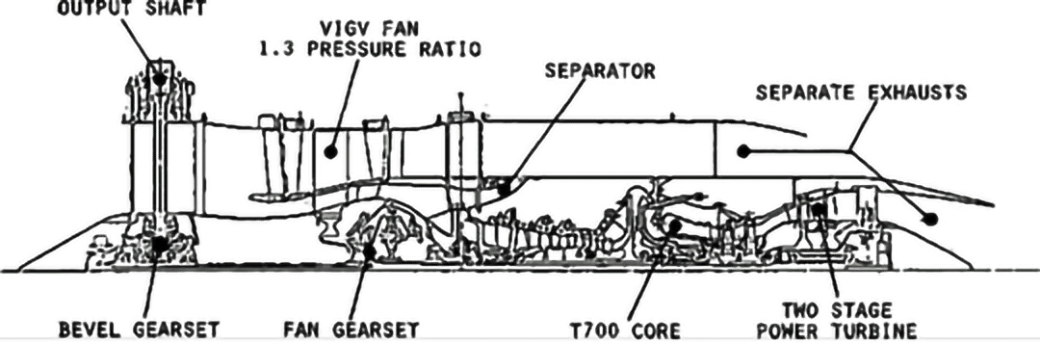
In a concurrent effort, NASA and DARPA funded General Electric to develop the GE CEST TF34 convertible engine. This was successfully designed and built and then tested at NASA Lewis from 1984 to 1986. It was a modified TF-34-400B engine and produced up to 7950 pounds of thrust with the inlet guide vanes open, and 4650 shp plus 1650 pounds of thrust with the inlet vanes fully closed. This photograph shows the engine being tested at the NASA Lewis (now Glenn) Research Center.
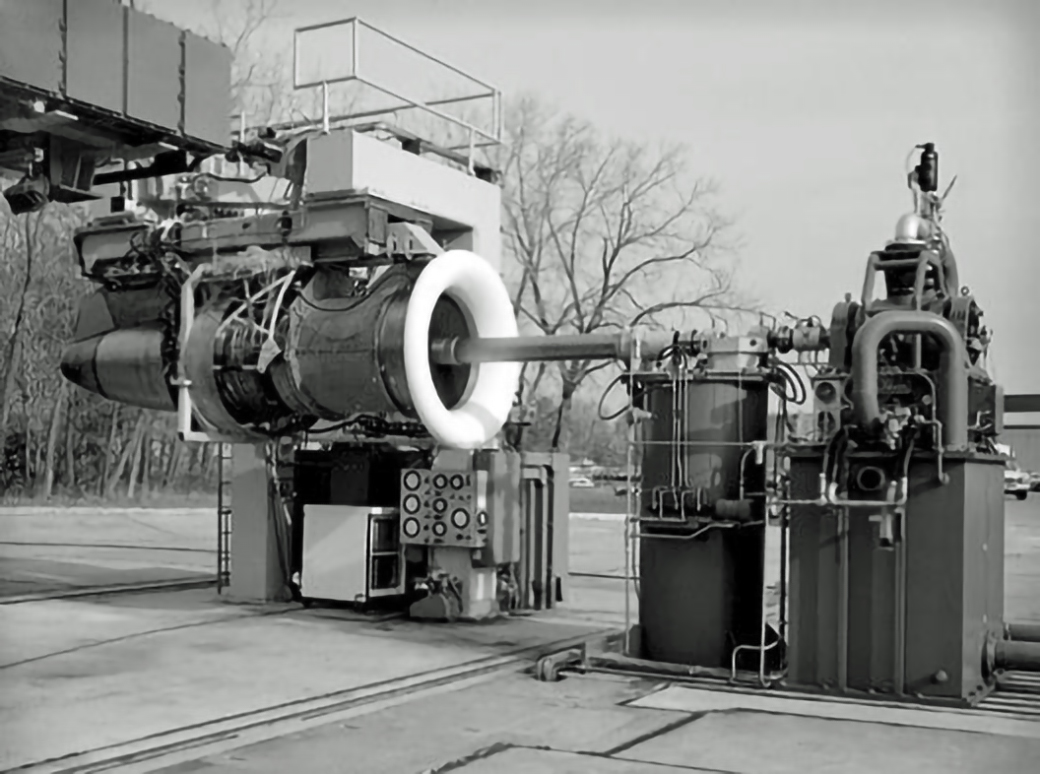
General Arrangement
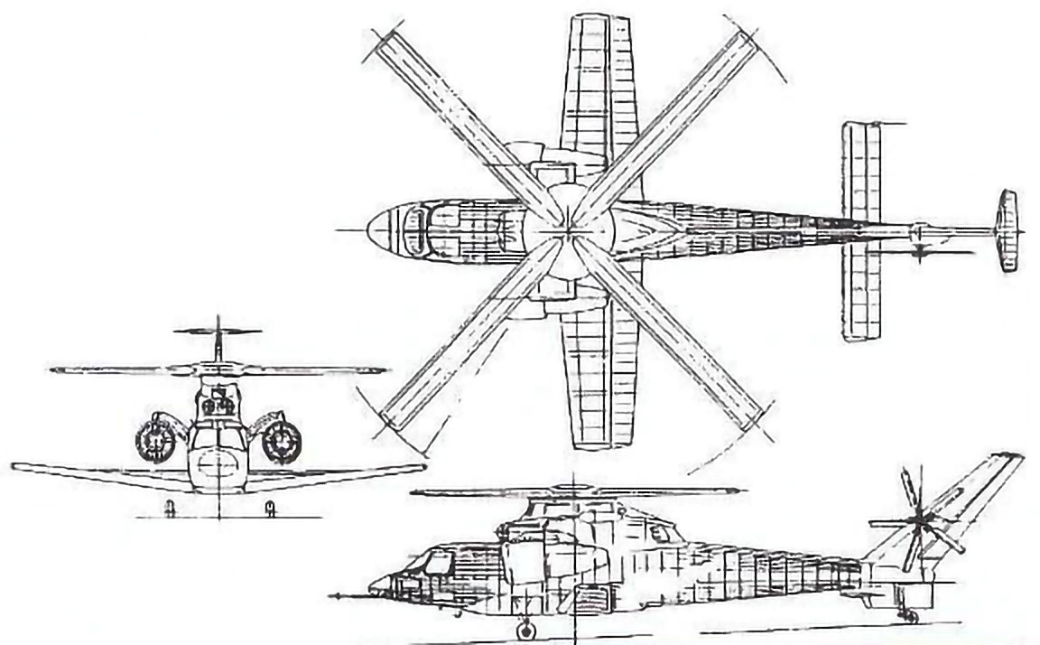
Characteristics and Performance
The X-Wing test hardware was developed for an aircraft with the following characteristics and performance:
Characteristics and Performance | |
---|---|
Design Gross Weight | 24,000 lbs. |
Rotor Diameter | 51 ft. |
No. of Blades | 4 |
Blade Chord | 3.39 ft. |
Disc Loading | 12 lbs./sq.ft. |
Demonstrator Aircraft Conceptual Designs
While the X-Wing hardware was being developed the design team was working on designs for the demonstrator aircraft. Numerous approaches were investigated including the use of the convertible engine to provide both shaft power for the X-Wing rotor and compressor and thrust for the high-speed fixed wing mode, as shown in the first illustration of this section. Another approach was to use conventional turboshaft engines to power both the X-Wing systems plus conventional propellers. Such a design with pusher propellers is shown below.
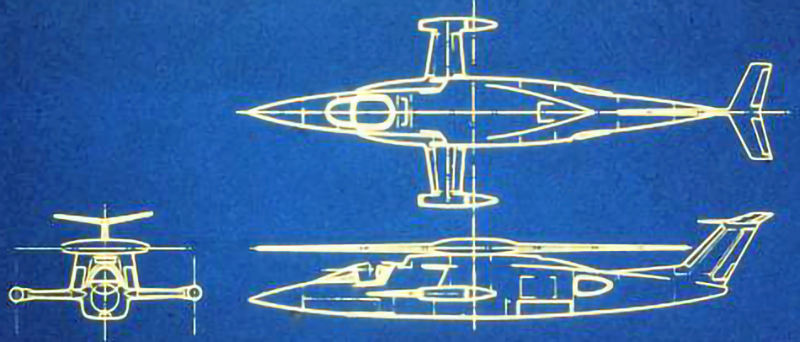
Production Aircraft Conceptual Design
Sikorsky also looked at a number of designs for potential production aircraft. One of these was a Navy aircraft to operate from the decks of DD963 class destroyers. X-Wing was thought to be applicable to missions that require high speed dash combined with short loiter or hover time, such as OTH (Over the Horizon) Targeting and Surveillance, and AFHSAR (Search and Rescue). This aircraft used a 50 ft. diameter rotor/wing and two General Electric GE-CTSF-34 high by-pass fan engines. Gross weight was 30,000 lbs. Anti-torque was provided by a nozzle at the tail vectoring the thrust of the engines. This design is shown below:
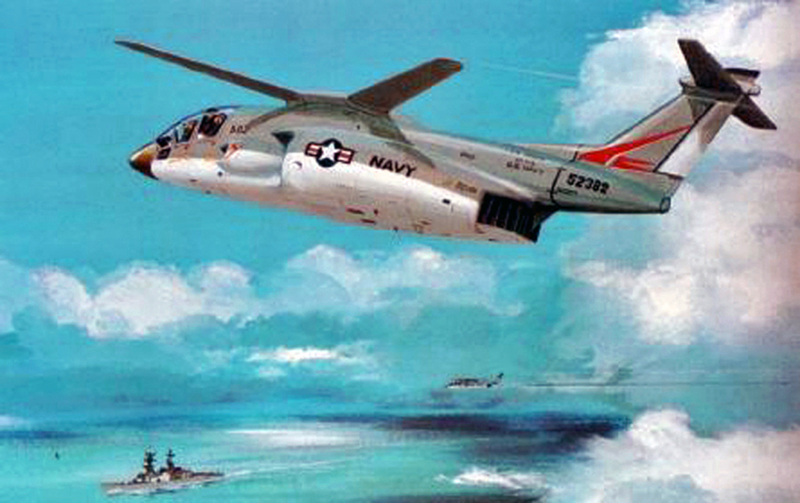
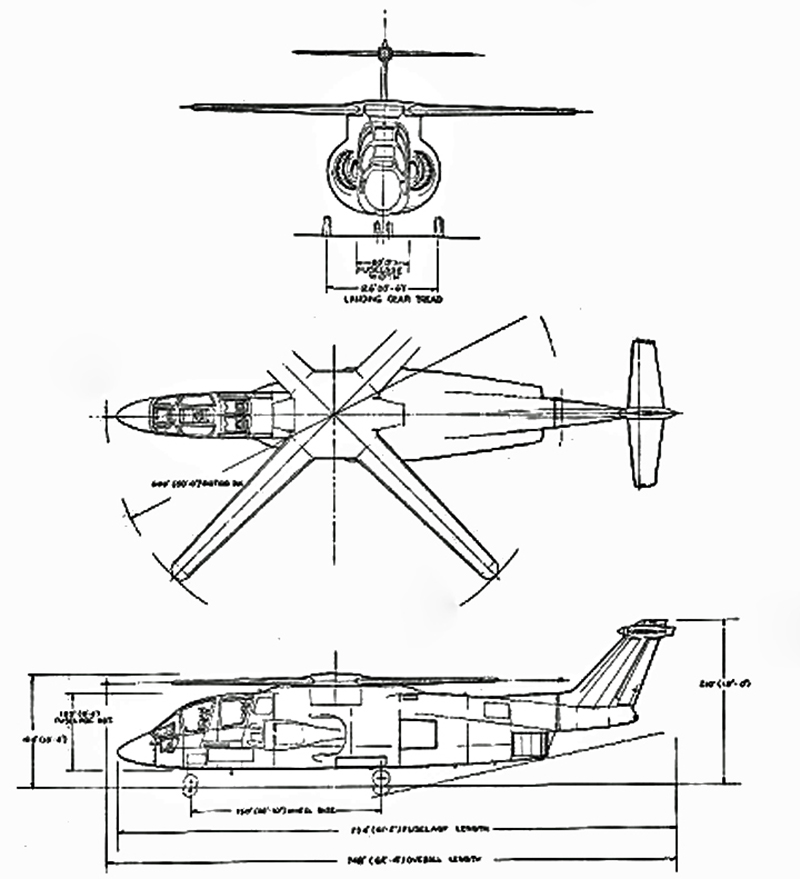
Concluding Remarks
At the time of termination the government had again reviewed the cost and risk of the program versus the potential of the X-Wing concept. It concluded that termination was in its best interest.
Over the five years of the contract, a tremendous amount of technical work had been accomplished and many difficult technical challenges had been resolved. The powered wind tunnel effort, plus compressor/clutch development, vehicle management system laboratory, system and software validation activities, composite material development, blade and rotor head fabrication, and appropriate risk mitigation tests were accomplished in a very few short years.
At the time of termination the X-Wing technology was still in the development stage. The true potential of the concept was not yet demonstrated in flight. Perhaps some day it will be demonstrated and a mission capable X-Wing will enter service.
With the X-Wing program Sikorsky gained much technical experience on bearingless composite rotors, and fly-by-wire and higher harmonic control systems, which greatly advanced these technologies for future aircraft.
Additional Information Resources
- Williams, Robert M., “X-Wing and the Navy V/STOL Initiative”, AIAA Student Journal, Winter 1982, page 26.
- “X-Wing Testbed Flies in Rotorless Configuration” Aviation Week and Space Technology, January 14, 1985
- Linden, A., Biggers, J., “X-Wing Potential for Navy Applications”, American Helicopter Society 41st Annual Forum, Fort Worth, Texas, May 1985.
- by Art Linden
by Art Linden, Dr Ken Rosen & Andy Whyte